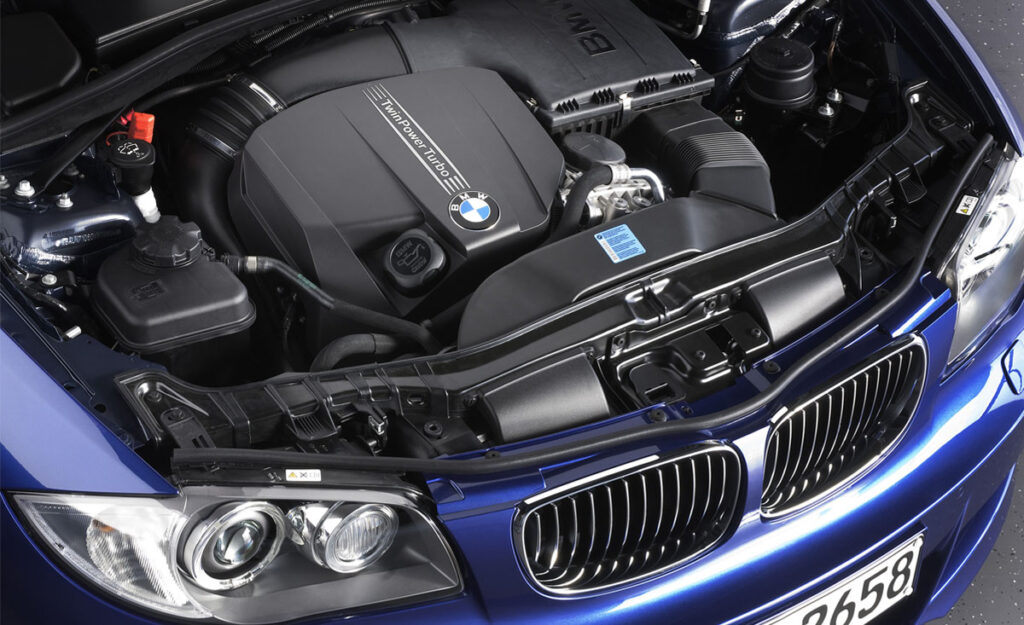
BMW’s TwinPower Turbo engines have been a mainstay in many of the automaker’s cars since their debut in the 2011 X1 xDrive28i.
Whether the vehicles were petrol or diesel, there is a good chance it would have incorporated TwinPower technology under the bonnet.
TwinPower Turbo might make it sound like the car has two turbos, but that is not the case.
What TwinPower refers to is rather the fitment of one “twin-scroll” turbo.
How it works
A twin-scroll turbo works similarly to a standard turbo, which sends more air into an engine to enhance power and efficiency.
In a standard turbo, however, one channel feeds gas from the exhaust manifold onto a turbine, whereas in a twin-scroll this is divided into two channels that direct air onto separate areas of the turbine blades.
The larger channel sends air onto the outside of the turbine blades, in turn causing the turbocharger to spool faster.
The smaller channel sends air to the inner area of the turbine blades, which improves turbo response – an attribute that is particularly helpful at low engine speeds.
The channels can be various sizes for different applications, but the basic concept remains.
This twin-scroll principle provides better low-rev response while simultaneously improving top-end power. Maximum output is reached at lower revs and lasts for longer, while power delivery is more responsive and linear.
The twin channels directed at the turbine can be seen in the below picture.
Variable geometry
Over the years, BMW’s engines have become much more complicated in the pursuit of performance and efficiency.
Alongside twin-scroll technologies, certain TwinPower Turbo diesel engines such as the one in the sixth-generation M550d xDrive use three-stage turbocharging with variable turbine geometry.
Variable turbine geometry refers to a set of fins inside the turbo – called vanes – which stand apart from the turbine itself. If these vanes are contracted they would form a closed circle around the turbine and allow nearly no airflow to reach the blades.
The vanes of the variable geometry turbocharger can be seen around the turbine in the photo below.
At low air volumes, the vanes adjust slightly to form V-shaped openings around the turbine for incoming air to be accelerated before hitting the turbine blades.
At high volumes, the vanes open wide to support increased airflow, while still compressing and accelerating everything that passes through them.
This serves to enhance the positive effects that the twin-scroll principles already bring.
According to a report by TorqueNews, the three-stage turbocharger used by BMW was a world first in 2012 and was produced specifically for the automaker’s diesel engines.
This turbocharger sees two small, high-pressure, variable geometry turbochargers mated with a larger low-pressure, water-cooled turbocharger.
The turbos activate at different engine speeds, thereby allowing the unit to generate higher boost in most situations and deliver consistent power.
Downsizing
Unfortunately, TwinPower Turbo technologies are one of the main reasons for BMW downsizing its engines over the past decade, as larger-displacement motors with many cylinders were simply not needed anymore.
It’s not all bad, however, as the smaller engines tended to produce more power, weigh less, and be more efficient than the ones they were replacing.
For example, the first TwinPower Turbo engine to make it to market in the 2011 X1 xDrive28i replaced a naturally-aspirated, 3.0-litre, six-cylinder unit.
While the six-cylinder might have produced 10kW more power than the 2.0-litre, four-cylinder TwinPower Turbo’s 180kW, the smaller engine generated 40Nm more torque – at 350Nm.
This resulted in a 0-100km/h time that was improved by 0.3 seconds for the automatic versions, as well as an average fuel consumption drop from 9.4l/100km to 7.9l/100km.